It is no secret that patient-specific cell therapies are widely perceived to be expensive to produce, which leads to expensive products, if they commercialize at all. I certainly agree that their production will be more expensive than protein-based therapies (how could they not be when, by definition, each product is specifically tailored for a patient?), but we have to keep in mind that, for the most part, today’s developers are seeking to create transformative, and quite possibly curative, therapies, rather than creating symptom management treatments for chronic diseases. We must hope and expect that there will be adequate value-based reimbursement in these scenarios.
The cost of manufacturing cell therapy products can nonetheless decrease through the employment of strategies that optimize manufacturing efficiency, leading to therapies that are not as expensive as analysts estimate today. However, the current state of cell therapy manufacturing processes is primarily one of manual labor and these processes are nowhere near what can be considered industrial-quality. Furthermore, to provide for both precision and sterility, these processes require bright, well-trained operators working in cleanrooms, leading to the burden of high labor and facilities costs.
Solutions are forming that address these challenges and we can guess where this will take us when we look at recent history. In the case of biologics, engineers went in and figured out how to scale them up. In the case of patient-specific immunotherapies we don’t, of course, scale up, but rather scale out. And today’s engineers are focused on that challenge.
When I spoke with reporter Angelo DePalma of BioProcess International for the magazine’s April 2016 Cancer Immunotherapy Special Report, I explained that it is this process of industrialization that is likely to transform the manufacturing of patient-specific cell therapies in the coming years. The industry’s solutions will lead to the factory of the future and a way to produce robust, quality, scalable and sustainable cell therapy products at a reasonable cost of goods. A development partner can facilitate this by standardizing and optimizing the unit operations of cell therapy one by one to get as close as possible to full automation and closed system manufacturing. In many cases, we can now start looking ahead to moving patient-specific cell therapy manufacturing out of the cleanroom.
Angelo wrote that “manufacturing is the critical – some might say existential – challenge for autologous cell-based immunotherapies.” I certainly agree, but in knowing the resources and attention that PCT and the industry are applying to this challenge, I fully believe it is one that can be overcome.
To read Angelo’s full article in BPI, click the button below:
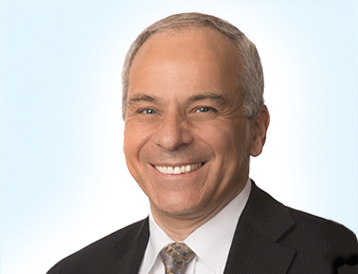